BUSINESS Our Business
Heat treatment
Heat treatment

Quenching/tempering
A common processing method that involves heating steel to austenitization and quenching it in oil. We also have a sub-zero device to suppress aging.

Vacuum hardening Solid solution treatment
This is a treatment method in which steel is heated to austenitization under reduced pressure and then rapidly cooled with N2 gas. It has high brightness and suppresses oxidation and decarburization.
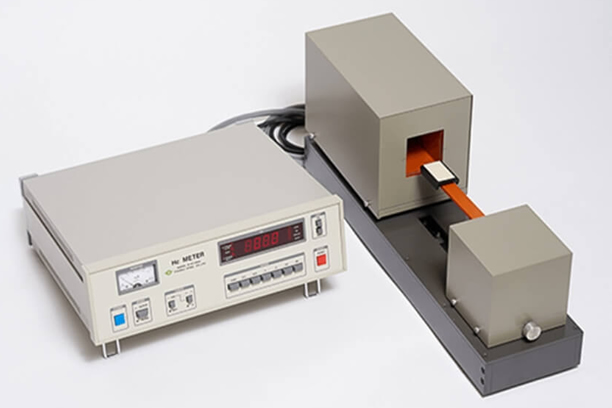
Annealing
The purpose is to adjust the holding power of soft magnetic materials. We have a HC meter and can measure coercive force.
Surface hardening treatment
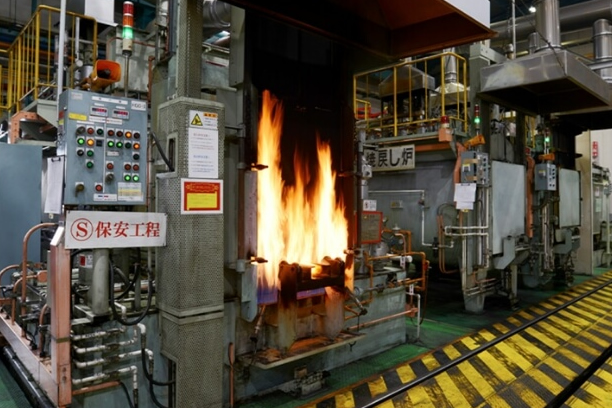
Carburizing/carbonitriding
This is a treatment method that infiltrates carbon/nitrogen. We will make optimal proposals by utilizing our extensive equipment lineup and the experience we have cultivated.
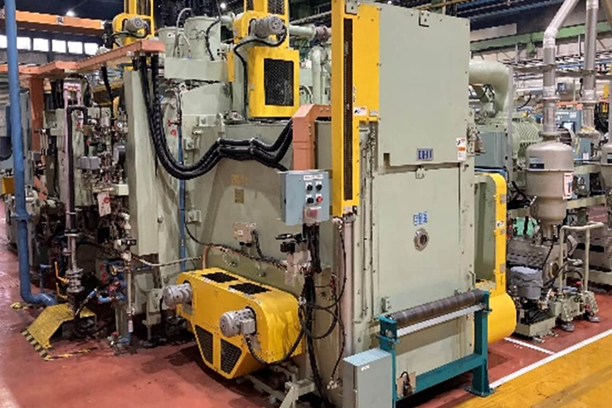
Vacuum carburizing (slow cooling)
Carburizing under reduced pressure can suppress the occurrence of grain boundary oxidation. In addition, slow cooling allows you to choose from a variety of secondary baking options.
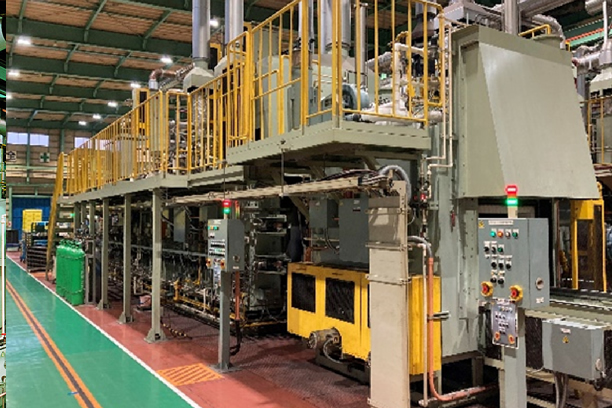
Gas nitrocarburizing
This is a treatment method that infiltrates nitrogen/carbon. Using our own know-how, we have succeeded in reducing the porous layer by up to 30%.
Special heat treatmentSpecial heat treatment
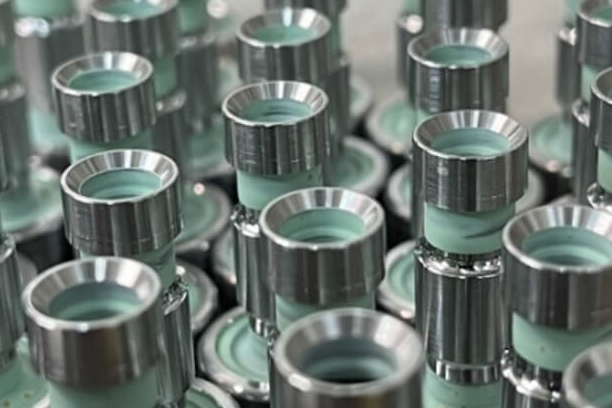
brazing
This is a method in which metal filler metal is brought into a molten state and joined by capillary action. Stable quality can be maintained by processing in a vacuum furnace.
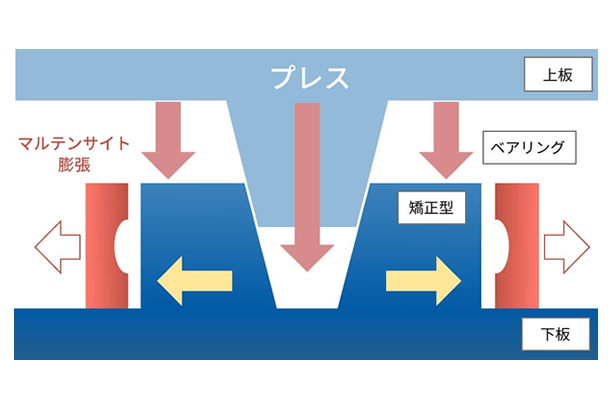
mild press quench
This is a press quenching method that takes advantage of the expansion during martensitic transformation after heating steel to austenitization and quenching it in oil. We mainly produce bearings.
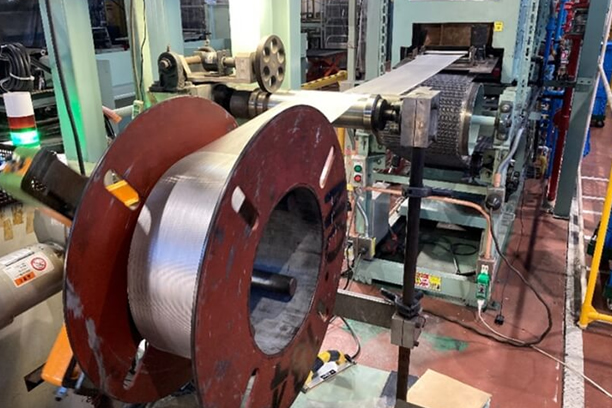
Hydrogen reduction Solid solution treatment
Using special equipment, we can produce thin roll shapes that cannot be produced using batch furnaces through solid solution treatment, normalizing, and annealing.
Thin film forming process
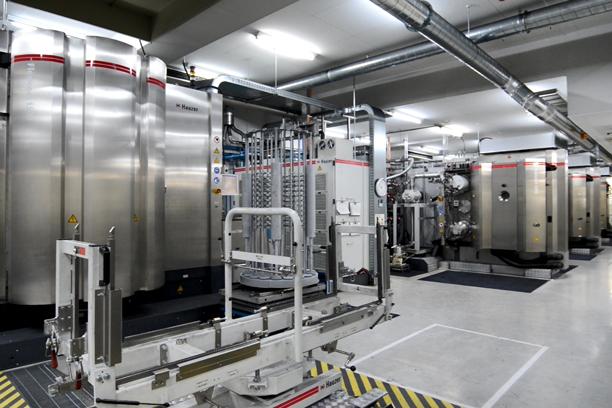
DLC coating (S-DLC, Me-DLC,C-DLC)
DLC stands for Diamond-Like Carbon, and this coating provides high tribological property. We develop and provide various coating films according to the needs of our customers.
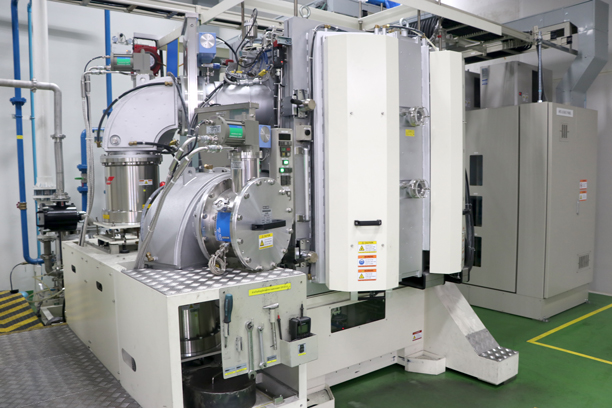
PVD coating (chrome type)
PVD coating (Physical Vapor Deposition) is roughly classified into chromium and titanium. A coating film containing chromium as the main element produces excellent sliding properties in oil,and has high hardness and heat resistance by adding other elements.
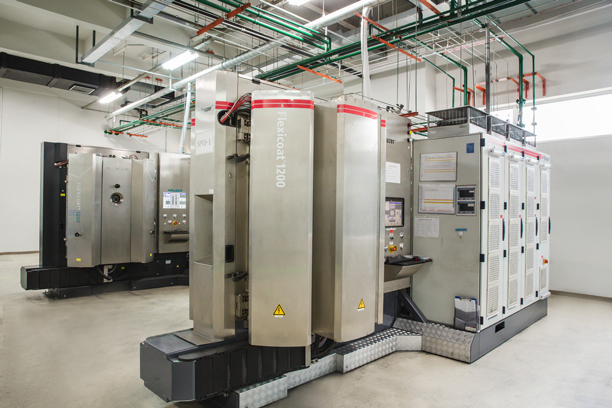
PVD coating (titanium type)
PVD coating (Physical Vapor Deposition) is roughly classified into chromium and titanium.Coating films containing titanium as the main element have excellent heat resistance and high hardness, and the addition of other elements extends the characteristics further.
Innovation business
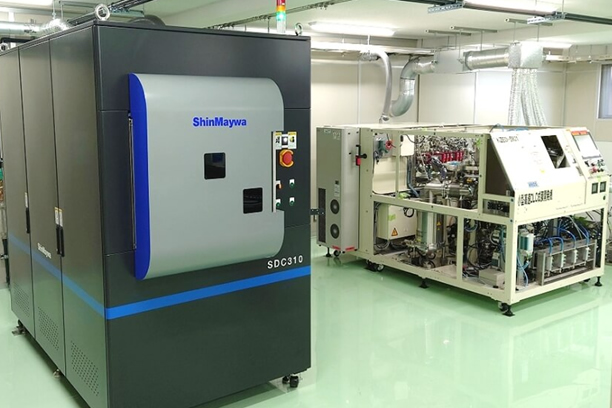
Open Innovation Center (O・I・C)
We have newly established the OIC area as a place to create new value using the latest technology and ideas centered on dry coating processing.
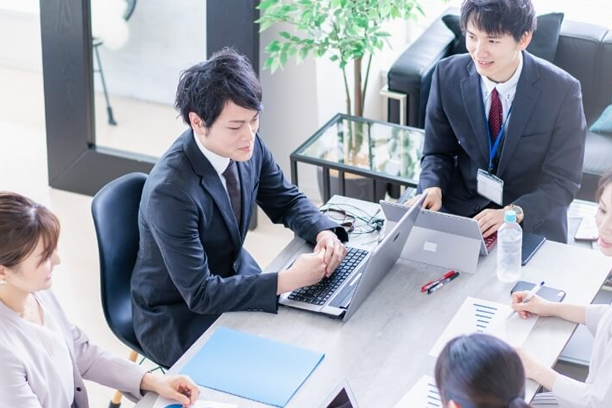
Joint research/joint work
The Innovation Division promotes joint development and joint work to develop technologies that meet market needs.